EcoFilter® 200
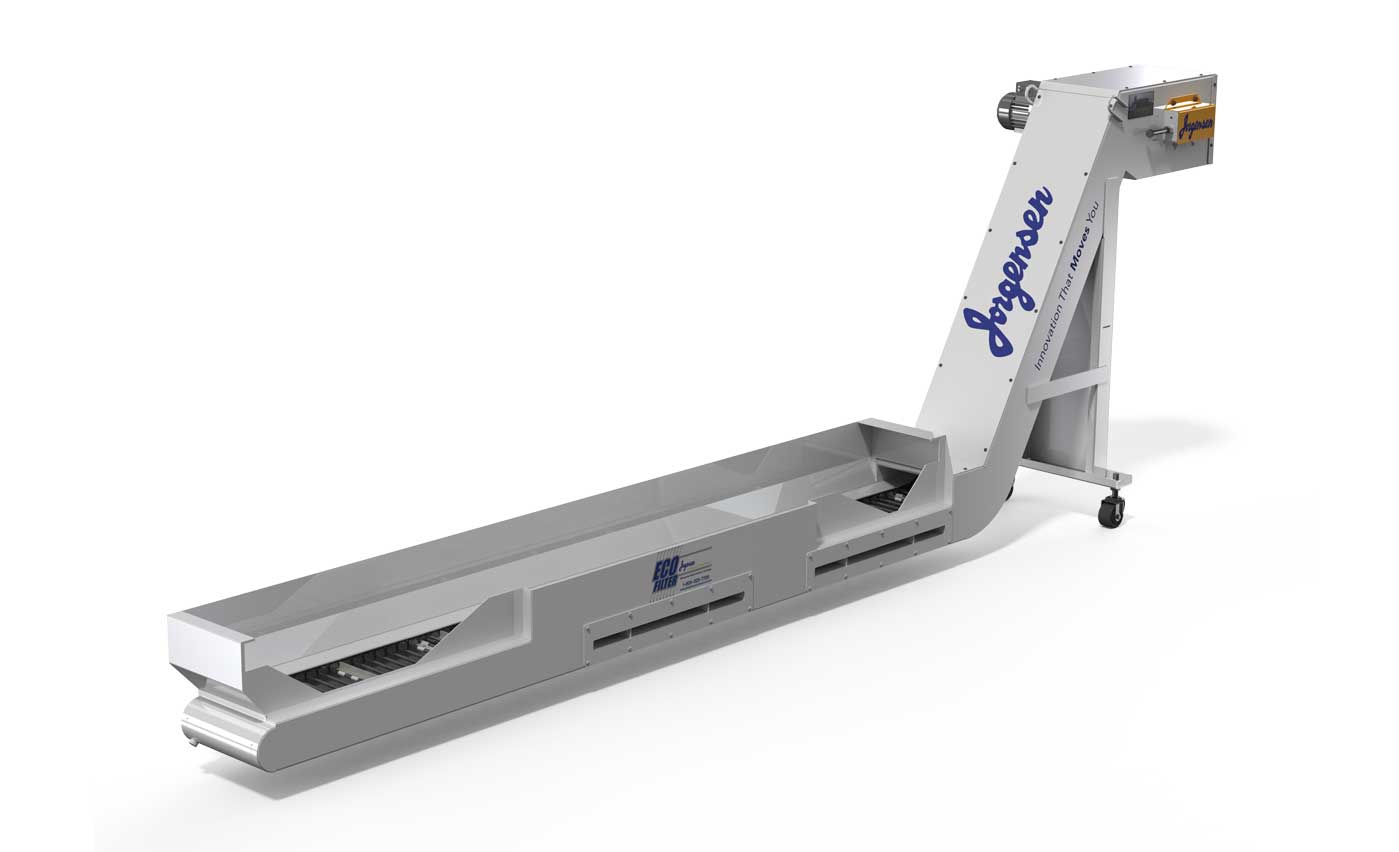
Filtering Conveyor Capable of 200-micron Filtration
EcoFilter® is a flexible, cost effective, self-cleaning conveyor and chip filtration system for turning and machining centers. It easily fits any machining center or lathe envelope. EcoFilter® conveyors accommodate a broad coolant flow rate range via flexible filter cell sizing. They provide efficient filtration of fine chips to 200-micron nominal at over 98% efficiency*, resulting in improved part finish and accuracy. EcoFilter® works well on its own or makes a great initial filtration option. It integrates especially well with FlexFiltration® systems.
How it Works
- Chips and coolant enter the conveyor’s load section.
- A hinged or scraper belt carries out large chips and/or stringers
- Coolant and fine chips flow to the section in between the runs of belt, where the EcoFilter® cell is located.
- The filter cell separates fine chips from coolant. Filtered coolant flows from the inside of the filter cell, out of the side of the conveyor, and into the coolant tank.
- Brushes continuously wipe fine chips from the surface of the filtration cell, keeping the cell clean for coolant to pass through.
- Small chips exit between the runs of belt through the bottom run via patent-pending CleanCleat® system, to the bottom of the conveyor casing.
- Fines that migrate to the bottom of the casing are scraped up to the top run of belt and discharged.
Jorgensen’s standard hinged steel belt “EcoFilter®-Ready” conveyors can convert to an EcoFilter® with a simple field retrofit kit within an estimated 4 hours.
If additional filtration is needed, EcoFilter® 80 is also available, capable of filtering down to 80-micron nominal.
*Third-party tested